Blender for the Pharmaceutical Market
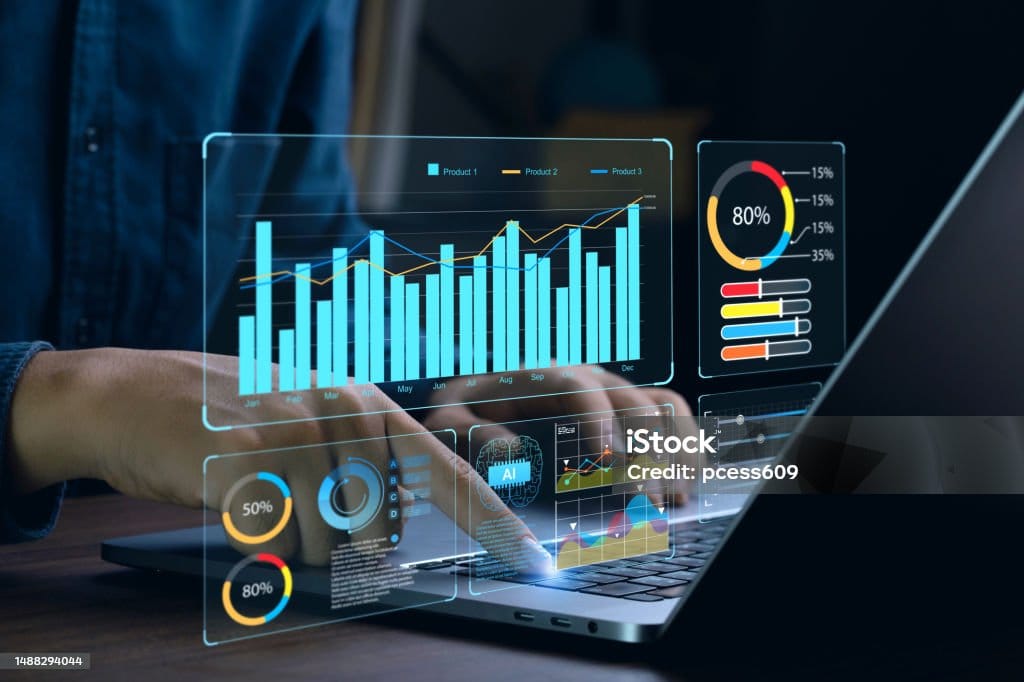
Blender for the Pharmaceutical Market Size and Forecast
The Blender for the Pharmaceutical Market was valued at USD 1.23 Billion in 2022 and is projected to reach USD 2.79 Billion by 2030, growing at a CAGR of 10.7% from 2024 to 2030. The demand for blenders in the pharmaceutical industry is driven by the increasing need for precision, efficiency, and scalability in drug formulation processes. These blenders are crucial for the production of powders, suspensions, and other dosage forms, facilitating better product quality and consistency. The growth of the market can be attributed to the expanding pharmaceutical manufacturing sector, along with advancements in technologies that improve blending processes. As pharmaceutical companies seek to streamline production, there is an increased adoption of automated and high-performance blenders across production lines.
Furthermore, the pharmaceutical industry’s rapid innovation in drug delivery systems and the rise of personalized medicine have created new opportunities for blending equipment. These advancements necessitate the development of specialized blenders that can handle a wide range of formulations. The market is expected to experience continued growth as regulatory standards tighten, pushing companies to invest in state-of-the-art blending solutions. With increasing focus on quality control and compliance, the demand for advanced blending technologies is anticipated to expand significantly in the coming years, further driving the market's positive outlook.
Download Full PDF Sample Copy of Market Report @
Blender for the Pharmaceutical Market Research Sample Report
Blender for the Pharmaceutical Market by Application
The Blender for the Pharmaceutical Market is a key equipment used in the processing and manufacturing of various pharmaceutical products. These blenders help in the uniform mixing of powders, granules, and liquids, ensuring consistency in product formulations. The pharmaceutical industry, with its stringent requirements for quality control and adherence to regulatory standards, uses blenders for several critical processes such as tablet formulation, capsule filling, and the production of oral suspensions, ointments, and creams. The growth of this market is fueled by advancements in blending technology, increasing demand for generic drugs, and the continuous expansion of the pharmaceutical sector in emerging markets.
Blenders for the pharmaceutical market are typically designed to meet high standards of hygiene and efficiency. The blending process in pharmaceuticals is essential not only for achieving consistent formulations but also for optimizing the active ingredient distribution. These machines are employed in the production of a variety of pharmaceutical forms, including solids, liquids, semi-solids, and powders. As the demand for high-quality pharmaceutical products rises, blenders with improved capabilities in terms of energy efficiency, automation, and cost-effectiveness are becoming essential for pharmaceutical manufacturers.
Pharmaceutical Industry Subsegment
The pharmaceutical industry segment of the blender market focuses on the use of blenders to manufacture a wide range of products including tablets, capsules, syrups, and injectables. The application of blenders in this area helps ensure that ingredients are evenly distributed throughout the product, which is crucial for both safety and efficacy. Blenders are commonly used in the initial stages of drug production where powders, active pharmaceutical ingredients (APIs), and excipients are mixed to form a homogenous blend, ready for further processing into tablets or capsules. The pharmaceutical sector’s focus on precision and quality is pushing demand for more advanced blending technologies to meet these needs.
In addition to the pharmaceutical products mentioned above, blenders in this segment are also used in the production of sterile injectables and topical formulations. As global health demands increase, especially in emerging markets, the pharmaceutical industry requires higher volumes of products with consistent quality, leading to an increase in the demand for more reliable and efficient blending solutions. Furthermore, the rise of biologics and biosimilars has increased the complexity of drug manufacturing processes, making the need for advanced blending technologies even more crucial. The pharmaceutical subsegment remains one of the largest and most significant contributors to the growth of the blender market.
Chemical Industry Subsegment
The chemical industry also represents a significant segment in the blender market, where the use of blenders helps create uniform mixtures of raw materials, chemicals, and other substances. In the chemical industry, blenders are crucial for processes such as the production of polymers, paints, coatings, adhesives, and other chemical products. The demand for blending solutions in this industry is driven by the need for consistency and precision in the formulation of chemical products, especially as regulations become more stringent and product quality expectations rise. Blenders are used in both the production of bulk materials and specialty chemicals that require high levels of uniformity and repeatability in their mixing processes.
Moreover, with the rise of green chemistry and sustainable practices, the chemical industry is increasingly adopting more efficient and environmentally friendly technologies. This has prompted the development of blenders that not only meet the high standards of mixing but also reduce energy consumption and waste. Additionally, the trend of digitalization in manufacturing, with the incorporation of advanced control systems, is transforming how blending operations are carried out in the chemical industry. The demand for automated systems that offer greater accuracy and less manual intervention is expected to continue to grow, driving the market for blenders in the chemical sector.
Key Trends and Opportunities in the Blender Market
Several key trends are currently shaping the Blender for the Pharmaceutical Market, creating new opportunities for innovation and growth. One significant trend is the shift towards automation and digitalization. As pharmaceutical manufacturers strive to increase operational efficiency and minimize human error, automated blending systems with advanced monitoring and control capabilities are in high demand. These systems are not only improving the consistency and accuracy of the blending process but also reducing production time and costs, making them highly attractive to pharmaceutical manufacturers. Additionally, as regulatory standards become more stringent, automated systems offer better documentation, ensuring compliance with industry regulations.
Another growing trend is the increasing demand for more sustainable blending solutions. In both the pharmaceutical and chemical industries, manufacturers are seeking to reduce their environmental footprint by adopting more energy-efficient machines and reducing waste during the blending process. This trend is fueling innovation in the design and functionality of blenders, with a focus on improving energy consumption, reducing noise levels, and minimizing the use of hazardous chemicals. Moreover, there is a rising emphasis on the production of personalized medicine, which is driving the need for smaller, more flexible blending systems that can accommodate the varying requirements of different drug formulations. These advancements present a significant opportunity for blender manufacturers to cater to niche markets and further penetrate the pharmaceutical and chemical sectors.
Frequently Asked Questions (FAQs)
What is a blender used for in the pharmaceutical industry?
A blender in the pharmaceutical industry is used to mix powders, granules, and liquids to create consistent and uniform drug formulations.
How do blenders contribute to drug manufacturing?
Blenders ensure that active pharmaceutical ingredients and excipients are evenly distributed throughout the product for consistent quality and efficacy.
What are the types of blenders used in pharmaceutical manufacturing?
The most common types include V-blenders, ribbon blenders, high-shear blenders, and double-c
For More Information or Query, Visit @ Blender for the Pharmaceutical Market Size And Forecast 2025-2030