Blow Molding Fuel Tank Market
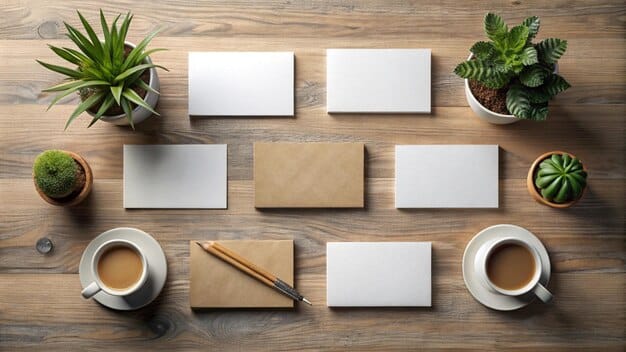
Blow Molding Fuel Tank Market Size and Forecast
The Blow Molding Fuel Tank Market was valued at USD 4.2 Billion in 2022 and is projected to reach USD 7.4 Billion by 2030, growing at a CAGR of 7.4% from 2024 to 2030. The increasing demand for lightweight and durable fuel tanks, combined with the growing adoption of blow molding technology in automotive and industrial applications, has significantly driven market growth. The shift towards environmentally friendly manufacturing processes and the growing adoption of electric vehicles (EVs) that require advanced fuel storage solutions are expected to support the expansion of the market in the coming years. Additionally, regulatory changes mandating fuel efficiency and reduced emissions further contribute to the demand for advanced fuel tank designs produced through blow molding techniques.
In terms of regional growth, the Blow Molding Fuel Tank Market in North America and Europe is anticipated to witness substantial growth due to the presence of leading automotive manufacturers and stringent environmental regulations. The Asia-Pacific region, particularly China and India, is also expected to experience significant growth, driven by the expanding automotive industry and increasing demand for fuel-efficient vehicles. The ongoing trend of replacing traditional metal fuel tanks with lightweight plastic variants is poised to further boost market development in the forecast period.
Download Full PDF Sample Copy of Market Report @
Blow Molding Fuel Tank Market Research Sample Report
Blow Molding Fuel Tank Market By Application
The Blow Molding Fuel Tank Market is primarily segmented by its application, which includes two key sectors: passenger vehicles and commercial vehicles. The growth in the automotive industry has driven the demand for fuel tanks, as they are integral to ensuring the functionality and safety of vehicles. Fuel tanks made through blow molding techniques offer several advantages, such as lightweight design, flexibility in shape, and durability, which are essential characteristics for both passenger and commercial vehicles. These tanks are typically made from high-density polyethylene (HDPE) or similar materials, which provide resistance to corrosion, reduce weight, and enhance fuel efficiency. As global automotive production increases, so does the need for fuel tanks, contributing to the expansion of the blow molding fuel tank market.This segment of the market is particularly impacted by growing automotive trends, including the shift toward electric vehicles (EVs) and the push for better fuel efficiency and lower emissions. For passenger vehicles, the demand is driven by the constant innovation in automotive manufacturing, including the need for stronger, lighter, and more efficient components. As environmental regulations tighten and automakers seek to meet stricter emission standards, the fuel tank market is evolving to incorporate advanced materials and design techniques. Additionally, the growing consumer demand for more fuel-efficient and affordable vehicles has further spurred innovation in fuel tank manufacturing. This presents opportunities for blow molding processes, which can produce cost-effective, high-quality fuel tanks that meet evolving market needs.
Passenger Vehicles
The passenger vehicle subsegment is one of the key drivers of the blow molding fuel tank market, owing to the high volume of automotive production and the significant demand for fuel storage solutions. These vehicles, including sedans, hatchbacks, and SUVs, rely on efficient and durable fuel tanks to ensure optimal fuel storage and vehicle performance. The design and production of fuel tanks for passenger vehicles have evolved to meet the increasing need for lightweight materials, reduced emissions, and enhanced safety features. Blow molding is a preferred manufacturing method because it allows for the creation of complex shapes and designs while maintaining a lightweight structure, which is crucial for improving fuel efficiency and reducing overall vehicle weight.With the growing consumer preference for more fuel-efficient vehicles, blow molding technology is being further refined to produce tanks that maximize fuel capacity while minimizing size and weight. The ongoing trend of producing eco-friendly vehicles with reduced environmental impact has also led to increased demand for blow molded fuel tanks, as manufacturers prioritize sustainable materials and production processes. Additionally, advancements in blow molding technology have enabled manufacturers to incorporate features like multi-layered tanks, which offer better fuel containment and protection. These innovations have become a key factor in attracting both manufacturers and consumers to opt for blow molded fuel tanks in the passenger vehicle market.
Commercial Vehicles
The commercial vehicle subsegment, which includes trucks, buses, and heavy-duty vehicles, is another major area driving the blow molding fuel tank market. Commercial vehicles have specific fuel storage needs, including larger tank capacities to support long-haul transportation and heavy-duty operations. Blow molding offers an efficient and cost-effective way to manufacture large, durable, and lightweight fuel tanks that meet the rigorous demands of commercial applications. The growing need for fuel-efficient, heavy-duty vehicles has contributed to the adoption of blow molded tanks, which not only reduce weight but also ensure durability and resistance to the harsh conditions faced by commercial vehicles in terms of wear and tear, exposure to various environmental elements, and mechanical stress.As the commercial vehicle industry continues to grow, especially with the rise of e-commerce and global supply chains, the demand for advanced fuel tanks in this segment is expected to increase. Furthermore, commercial vehicle manufacturers are under pressure to meet stringent emissions standards and fuel efficiency regulations. Blow molded fuel tanks provide an ideal solution, offering benefits such as reduced weight, increased fuel efficiency, and enhanced safety. These factors are contributing to the increasing adoption of blow molding technology in commercial vehicle manufacturing, which is expected to drive the growth of the fuel tank market within this subsegment.
Key Trends and Opportunities in the Market
Several key trends and opportunities are shaping the future of the blow molding fuel tank market. One of the most prominent trends is the increasing demand for lightweight fuel tanks, driven by the global push for improved fuel efficiency and reduced carbon emissions. As manufacturers seek to meet stricter environmental regulations, blow molding has emerged as a preferred method for creating lightweight yet durable fuel tanks. The material choices for blow molded tanks, such as high-density polyethylene (HDPE), also offer resistance to corrosion and ensure longevity, further fueling the market’s growth.Another notable trend is the shift towards sustainable and eco-friendly materials in fuel tank production. As consumers and manufacturers become more environmentally conscious, there is a growing emphasis on the use of recyclable and non-toxic materials. This has created opportunities for innovation in the development of bio-based plastics and other sustainable alternatives to traditional materials used in fuel tank manufacturing. Additionally, the rise of electric vehicles (EVs) presents both challenges and opportunities for the blow molding fuel tank market, as manufacturers explore ways to integrate new technologies, such as hybrid powertrains and advanced battery systems, which require more complex and customized fuel tank solutions.
As the automotive industry continues to evolve, there are significant opportunities for the blow molding fuel tank market to expand, particularly as new technologies and design innovations emerge. The push for fuel-efficient and low-emission vehicles, coupled with the increasing demand for commercial and electric vehicles, is expected to create a growing need for advanced fuel storage solutions. Furthermore, the ongoing trend towards customization and personalized vehicle designs offers manufacturers the opportunity to leverage blow molding technology to create highly tailored and unique fuel tanks that meet specific customer requirements. Overall, these trends indicate a positive outlook for the blow molding fuel tank market, with a variety of opportunities for growth and innovation in the coming years.
Frequently Asked Questions
What is blow molding, and how is it used in fuel tank production?
Blow molding is a manufacturing process used to produce hollow plastic parts by inflating a heated plastic tube inside a mold. It is commonly used to create fuel tanks due to its ability to produce complex shapes efficiently.
What materials are typically used in blow molding fuel tanks?
High-density polyethylene (HDPE) is the most commonly used material for blow molded fuel tanks due to its strength, lightweight nature, and resistance to corrosion and chemicals.
Why is blow molding preferred for fuel tank production?
Blow molding is preferred because it allows for the production of lightweight, durable, and complex-shaped tanks at lower production costs compared to other manufacturing methods.
What are the key applications of blow molded fuel tanks?
The key applications of blow molded fuel tanks include passenger vehicles, commercial vehicles, and heavy-duty transportation vehicles, as they require robust and lightweight fuel storage solutions.
How does blow molding contribute to fuel efficiency in vehicles?
Blow molding produces lighter fuel tanks, reducing the overall vehicle weight and improving fuel efficiency. Lighter vehicles require less energy to move, which translates to lower fuel consumption.
Are blow molded fuel tanks more environmentally friendly?
Yes, blow molded fuel tanks are made from recyclable materials like HDPE, and the manufacturing process itself is energy-efficient, contributing to lower environmental impact.
What are the main benefits of using blow molded fuel tanks in commercial vehicles?
Blow molded fuel tanks are lightweight, durable, and resistant to corrosion, making them ideal for commercial vehicles that endure heavy usage and harsh conditions.
Can blow molding technology be applied to electric vehicles (EVs)?
Yes, blow molding technology can be applied to electric vehicles, especially in the production of components like lightweight battery casings and fluid reservoirs in hybrid or electric powertrains.
How do trends in fuel efficiency impact the blow molding fuel tank market?
As consumers and manufacturers demand more fuel-efficient vehicles, the need for lightweight, durable, and high-capacity fuel tanks drives growth in the blow molding fuel tank market.
What future opportunities exist for the blow molding fuel tank market?
The growing adoption of electric and hybrid vehicles, coupled with trends in sustainability and fuel efficiency, presents numerous opportunities for innovation and market expansion in the blow molding fuel tank sector.
For More Information or Query, Visit @ Blow Molding Fuel Tank Market Size And Forecast 2025-2030
Blow Molding Fuel Tank Market Size and Forecast
The Blow Molding Fuel Tank Market was valued at USD 4.2 Billion in 2022 and is projected to reach USD 7.4 Billion by 2030, growing at a CAGR of 7.4% from 2024 to 2030. The increasing demand for lightweight and durable fuel tanks, combined with the growing adoption of blow molding technology in automotive and industrial applications, has significantly driven market growth. The shift towards environmentally friendly manufacturing processes and the growing adoption of electric vehicles (EVs) that require advanced fuel storage solutions are expected to support the expansion of the market in the coming years. Additionally, regulatory changes mandating fuel efficiency and reduced emissions further contribute to the demand for advanced fuel tank designs produced through blow molding techniques.
In terms of regional growth, the Blow Molding Fuel Tank Market in North America and Europe is anticipated to witness substantial growth due to the presence of leading automotive manufacturers and stringent environmental regulations. The Asia-Pacific region, particularly China and India, is also expected to experience significant growth, driven by the expanding automotive industry and increasing demand for fuel-efficient vehicles. The ongoing trend of replacing traditional metal fuel tanks with lightweight plastic variants is poised to further boost market development in the forecast period.
Download Full PDF Sample Copy of Market Report @
Blow Molding Fuel Tank Market Research Sample Report
Blow Molding Fuel Tank Market By Application
The Blow Molding Fuel Tank Market is primarily segmented by its application, which includes two key sectors: passenger vehicles and commercial vehicles. The growth in the automotive industry has driven the demand for fuel tanks, as they are integral to ensuring the functionality and safety of vehicles. Fuel tanks made through blow molding techniques offer several advantages, such as lightweight design, flexibility in shape, and durability, which are essential characteristics for both passenger and commercial vehicles. These tanks are typically made from high-density polyethylene (HDPE) or similar materials, which provide resistance to corrosion, reduce weight, and enhance fuel efficiency. As global automotive production increases, so does the need for fuel tanks, contributing to the expansion of the blow molding fuel tank market.This segment of the market is particularly impacted by growing automotive trends, including the shift toward electric vehicles (EVs) and the push for better fuel efficiency and lower emissions. For passenger vehicles, the demand is driven by the constant innovation in automotive manufacturing, including the need for stronger, lighter, and more efficient components. As environmental regulations tighten and automakers seek to meet stricter emission standards, the fuel tank market is evolving to incorporate advanced materials and design techniques. Additionally, the growing consumer demand for more fuel-efficient and affordable vehicles has further spurred innovation in fuel tank manufacturing. This presents opportunities for blow molding processes, which can produce cost-effective, high-quality fuel tanks that meet evolving market needs.
Passenger Vehicles
The passenger vehicle subsegment is one of the key drivers of the blow molding fuel tank market, owing to the high volume of automotive production and the significant demand for fuel storage solutions. These vehicles, including sedans, hatchbacks, and SUVs, rely on efficient and durable fuel tanks to ensure optimal fuel storage and vehicle performance. The design and production of fuel tanks for passenger vehicles have evolved to meet the increasing need for lightweight materials, reduced emissions, and enhanced safety features. Blow molding is a preferred manufacturing method because it allows for the creation of complex shapes and designs while maintaining a lightweight structure, which is crucial for improving fuel efficiency and reducing overall vehicle weight.With the growing consumer preference for more fuel-efficient vehicles, blow molding technology is being further refined to produce tanks that maximize fuel capacity while minimizing size and weight. The ongoing trend of producing eco-friendly vehicles with reduced environmental impact has also led to increased demand for blow molded fuel tanks, as manufacturers prioritize sustainable materials and production processes. Additionally, advancements in blow molding technology have enabled manufacturers to incorporate features like multi-layered tanks, which offer better fuel containment and protection. These innovations have become a key factor in attracting both manufacturers and consumers to opt for blow molded fuel tanks in the passenger vehicle market.
Commercial Vehicles
The commercial vehicle subsegment, which includes trucks, buses, and heavy-duty vehicles, is another major area driving the blow molding fuel tank market. Commercial vehicles have specific fuel storage needs, including larger tank capacities to support long-haul transportation and heavy-duty operations. Blow molding offers an efficient and cost-effective way to manufacture large, durable, and lightweight fuel tanks that meet the rigorous demands of commercial applications. The growing need for fuel-efficient, heavy-duty vehicles has contributed to the adoption of blow molded tanks, which not only reduce weight but also ensure durability and resistance to the harsh conditions faced by commercial vehicles in terms of wear and tear, exposure to various environmental elements, and mechanical stress.As the commercial vehicle industry continues to grow, especially with the rise of e-commerce and global supply chains, the demand for advanced fuel tanks in this segment is expected to increase. Furthermore, commercial vehicle manufacturers are under pressure to meet stringent emissions standards and fuel efficiency regulations. Blow molded fuel tanks provide an ideal solution, offering benefits such as reduced weight, increased fuel efficiency, and enhanced safety. These factors are contributing to the increasing adoption of blow molding technology in commercial vehicle manufacturing, which is expected to drive the growth of the fuel tank market within this subsegment.
Key Trends and Opportunities in the Market
Several key trends and opportunities are shaping the future of the blow molding fuel tank market. One of the most prominent trends is the increasing demand for lightweight fuel tanks, driven by the global push for improved fuel efficiency and reduced carbon emissions. As manufacturers seek to meet stricter environmental regulations, blow molding has emerged as a preferred method for creating lightweight yet durable fuel tanks. The material choices for blow molded tanks, such as high-density polyethylene (HDPE), also offer resistance to corrosion and ensure longevity, further fueling the market’s growth.Another notable trend is the shift towards sustainable and eco-friendly materials in fuel tank production. As consumers and manufacturers become more environmentally conscious, there is a growing emphasis on the use of recyclable and non-toxic materials. This has created opportunities for innovation in the development of bio-based plastics and other sustainable alternatives to traditional materials used in fuel tank manufacturing. Additionally, the rise of electric vehicles (EVs) presents both challenges and opportunities for the blow molding fuel tank market, as manufacturers explore ways to integrate new technologies, such as hybrid powertrains and advanced battery systems, which require more complex and customized fuel tank solutions.
As the automotive industry continues to evolve, there are significant opportunities for the blow molding fuel tank market to expand, particularly as new technologies and design innovations emerge. The push for fuel-efficient and low-emission vehicles, coupled with the increasing demand for commercial and electric vehicles, is expected to create a growing need for advanced fuel storage solutions. Furthermore, the ongoing trend towards customization and personalized vehicle designs offers manufacturers the opportunity to leverage blow molding technology to create highly tailored and unique fuel tanks that meet specific customer requirements. Overall, these trends indicate a positive outlook for the blow molding fuel tank market, with a variety of opportunities for growth and innovation in the coming years.
Frequently Asked Questions
What is blow molding, and how is it used in fuel tank production?
Blow molding is a manufacturing process used to produce hollow plastic parts by inflating a heated plastic tube inside a mold. It is commonly used to create fuel tanks due to its ability to produce complex shapes efficiently.
What materials are typically used in blow molding fuel tanks?
High-density polyethylene (HDPE) is the most commonly used material for blow molded fuel tanks due to its strength, lightweight nature, and resistance to corrosion and chemicals.
Why is blow molding preferred for fuel tank production?
Blow molding is preferred because it allows for the production of lightweight, durable, and complex-shaped tanks at lower production costs compared to other manufacturing methods.
What are the key applications of blow molded fuel tanks?
The key applications of blow molded fuel tanks include passenger vehicles, commercial vehicles, and heavy-duty transportation vehicles, as they require robust and lightweight fuel storage solutions.
How does blow molding contribute to fuel efficiency in vehicles?
Blow molding produces lighter fuel tanks, reducing the overall vehicle weight and improving fuel efficiency. Lighter vehicles require less energy to move, which translates to lower fuel consumption.
Are blow molded fuel tanks more environmentally friendly?
Yes, blow molded fuel tanks are made from recyclable materials like HDPE, and the manufacturing process itself is energy-efficient, contributing to lower environmental impact.
What are the main benefits of using blow molded fuel tanks in commercial vehicles?
Blow molded fuel tanks are lightweight, durable, and resistant to corrosion, making them ideal for commercial vehicles that endure heavy usage and harsh conditions.
Can blow molding technology be applied to electric vehicles (EVs)?
Yes, blow molding technology can be applied to electric vehicles, especially in the production of components like lightweight battery casings and fluid reservoirs in hybrid or electric powertrains.
How do trends in fuel efficiency impact the blow molding fuel tank market?
As consumers and manufacturers demand more fuel-efficient vehicles, the need for lightweight, durable, and high-capacity fuel tanks drives growth in the blow molding fuel tank market.
What future opportunities exist for the blow molding fuel tank market?
The growing adoption of electric and hybrid vehicles, coupled with trends in sustainability and fuel efficiency, presents numerous opportunities for innovation and market expansion in the blow molding fuel tank sector.
For More Information or Query, Visit @ Blow Molding Fuel Tank Market Size And Forecast 2025-2030